Many UBC tech-based startups progress through entrepreneurship@UBC (e@UBC) intake programs and graduate to the HATCH accelerator in the Institute for Computing, Information and Cognitive Systems (ICICS). There they receive the mentorship, intern support, and investor access that helps them succeed. Now, thanks to the support of donors, they can refine their prototypes in a fully equipped makerspace.
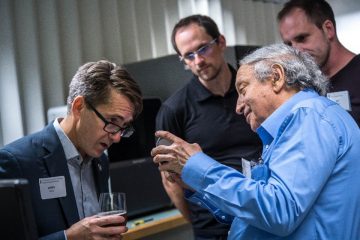
Rapidia founder Dan Gelbart explains his unique 3D metal printer to Applied Science Dean James Olson
A 3D metal printer purchased with this funding, for example, will allow HATCH ventures to safely and economically create metal parts and prototypes and refine their products. In conventional 3D metal printing, a paste comprising metal particles and a polymer support material is emitted from a nozzle to form the part. Usually the support material is removed through a chemical “de-binding” process and baked in a furnace, leaving the metal part. The off-gases must be removed through external ventilation. The polymer and solvent then need to be disposed of safely, as they are hazardous materials and not biodegradable.
The new machine, from Vancouver company Rapidia, uniquely uses a water-based metal paste. Once the object is printed, it is heated in a “furnace” to evaporate the water, uniformly shrinking the part by roughly 10% to leave the finished part. No fumes or odours are emitted during printing, other than water vapour. Therefore, no external ventilation is required, and there are no hazardous byproducts to dispose of. This also significantly reduces operating costs, since the water-based paste is cheaper than the polymer-based paste, and no additional de-binding chemicals need to be purchased. Reduced metal usage in the Rapidia process also lowers prototyping costs, a significant concern for startups.
The Rapidia machine was invented by UBC honorary professor and occasional instructor Dan Gelbart, who holds over 100 U.S. patents. Gelbart is considered the father of modern computer-to-plate printing technology, where the intermediate film step is removed, saving costs and chemical usage. The technology was commercialized by the hugely successful Burnaby-based company Creo, which Gelbart co-founded and was bought by Eastman Kodak in 2005 for roughly $1 billion.
Donor funding has also enabled the purchase of a state-of-the-art handheld 3D scanner for virtualizing objects. These can then be modified and 3D printed, or used to gather data. What is unique about this model from Artec Leo is that the user can do an overall scan then go back and fill in details. Processing is done onboard, so no external computing power is required.
The new scanner was recently used by research scientists from Canada’s particle accelerator centre TRIUMF and UBC’s Engineering Physics Project Lab to virtualize vessels containing single-photon sensors. These can be used to detect neutrinos in the new Hyper-Kamiokande (Hyper-K) neutrino observatory to be built near Kamioka, Japan, and become operational in 2027. Hyper-K is part of an international collaboration including Canada, and will be the successor to the current Nobel Prize-winning Super-K observatory, also in Japan.
Neutrinos are intriguing as they can shed light on the origins of the universe, solar and astronomical processes, and some fundamental problems in particle physics. However, since they usually pass through matter unaffected, their presence must be detected by rare interactions with other particles. For example, a neutrino interaction with a nucleus in water can produce an electron that creates a cone of radiation light. In Hyper-K, this light is recorded by the photosensors, allowing researchers to infer the kinematics and type of incoming neutrino.
Hyper-K will have a water tank with almost 200 million litres of ultrapure water, buried 650 meters deep to reduce interference from cosmic radiation. Thousands of these photosensor vessels are envisioned to line the walls of the tank. By virtualizing the the components of the vessels in the HATCH makerspace, the TRIUMF and UBC team hope to establish a good fit, since the vessels will need to be waterproof and withstand extreme pressures.
Funding from donors has also allowed HATCH to purchase an oscilloscope for electronics testing. UBC had the chance to formally thank the donors when the HATCH makerspace was officially launched in late 2019.