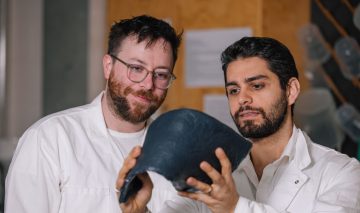
Jordan MacKenzie (L) and Bioform Lead Design Engineer Rami Younes with a sheet of Bioform’s bioplastic. Photo credit: Michael Buchen, Bioform
The first man-made plastic was demonstrated at the 1862 Great International Exhibition in London. Once heated, the material could be molded and retained its shape when cooled. Since it was made from cellulose, it led to a product called celluloid, which was used for billiard balls and the first flexible photographic film.
Fast forward to the 1950s and the birth of the plastics industry, leading to ubiquitous use of petroleum-based plastics for consumer and industrial products, with global production reaching 400 million tonnes a year in 2021.
But components of the first plastics are still with us, having broken down to micro- and nano-plastics. These small particles never fully decompose and are found in water, soil, and air around the globe, including in polar ice and in the deepest places on Earth. These particles are ingested by us and other animals, and can spread throughout the body. The health effects of this are not yet fully understood.
In the ocean, plastic pollution has created a “plastic soup” of small, pepper-like particles that accumulate due to currents, such as in the Great Pacific Garbage Patch. As microplastics and other trash collect on or near the surface of the ocean, they block sunlight from reaching plankton and algae below, which threatens the entire ocean food chain. It is estimated that we are adding as much as 13 million tonnes of plastic to the ocean every year.
Finding a Solution in Nature
Would-be entrepreneurs are trained by startup accelerator programs to create solutions to known problems, rather than developing solutions that need a problem. Bioform Technologies, a UBC startup in the HATCH Venture Builder program in ICICS, is ambitiously tackling plastics pollution, one of the biggest problems we face globally, by developing a fully biodegradable replacement.
The brainchild of Bioform CEO, CTO, and co-founder Jordan MacKenzie, the company’s plastic alternative revisits plastic’s cellulose-based origins by combining feedstocks of wood pulp fibre and kelp with a salt-based catalyst in an extrusion printing process similar to that used in papermaking. MacKenzie developed the process when he was a postdoctoral fellow and then research associate at UBC in the lab of Chemical and Biological Engineering professor and Bioform co-founder Mark Martinez. As a past director of UBC’s Pulp and Paper Centre, Martinez was an ideal supervisor and collaborator for MacKenzie over the many years of research that led to Bioform.
“Our initial work was focused on a classic problem in fluid dynamics—how do you put two fluids on top of one another, flow them really fast and prevent them from mixing?” says MacKenzie. “It still amazes me that our solution to such an old problem is so well suited to manufacturing sustainable alternatives to plastic.”
The patented Bioform process involves a sequence of printing the feedstock of pulp fibre, kelp, and salt mixture in layers, while leaving a high water content. It is then pressed to the desired water content for specific products. Higher water content provides a softer, more flexible material suitable for products like bioplastic films, while lower water content yields a more rigid material for products like container lids or trays. Finally, the product is molded to desired shapes.
Biodegradable Bioplastics and Renewable Feedstocks
The beauty of the Bioform product is that the wood pulp fibre and kelp feedstocks are renewable, and the bioplastic produced biodegrades in as little as six months, enriching the environment with nutrients rather than degrading it. Kelp, which contains natural polymers essential for bioplastics, grows up to 60 cm per day, allowing several harvests annually from commercial kelp farms. Wood pulp fibre is readily available from trees grown for forestry operations, which can be harvested every 8-12 years. The icing on the cake is that the cost of producing the Bioform product is comparable to that of conventional plastic—there is no “green premium”.
Initial Target Products
Agriculture is a major plastic consumer, since sheets of plastic are often used as mulch, rather than natural materials such as wood chips. Plastic mulch film is used to control weeds and protect crops during cold winter months. It also preserves soil nutrients and helps prevent erosion. As a result, it is widely used. Unfortunately, the mulch film ends up in landfills, and requires significant labour to remove it from fields and transport it there.
Bioform has created a mulch film that is biodegradable, so it doesn’t have to be removed in the spring, and contributes to soil nutrients as it decomposes. As the film dries in the field, it stiffens, further protecting crops. The Bioform mulch has been tested on research crops at UBC and proven to be effective.
The company’s bioplastic also lends itself well to consumer and food packaging, a major source of plastic pollution. With the appropriate stiffness, it can be molded into disposable food utensils, whose use skyrocketed during the Covid pandemic.
With plastics in such wide use, the potential applications of Bioform’s plastic alternative are virtually endless.
“We’ve put a significant amount of effort into developing compositions of matter that can stand up against the performance of fossil fuel-based plastics,” says MacKenzie. “Now, we’re able to modify our process to produce a wide range of consumer packaging products, like bottles.”
Bioform plans to move on from its springboard in HATCH to its own commercial space in the near future. The company’s potential was recognized when Bioform was chosen as one of the finalists for the 2022 Ocean Changemaker Challenge, based on the their video submission. If everything goes as planned, we should see Bioform bioplastics replacing plastic products before long, helping to tilt the world in the right direction.